| Casting About, from Al to ZincThe best metal for the job isn't always the ideal one. |
| |
| |
The great corn breeder John Laughnan used to say that the soil and climate of Champaign County, Illinois, were the best in the world for growing corn, but that they were not ideal. That is, given a chance, he could design a plot of land and a climate that would grow corn even better.
I feel the same way about elements. Iron is the best for building bridges, because it's very strong and very cheap, and it's easy to weld and machine. But it's not ideal: It rusts. The fact that iron is reactive and unstable in air is one of the great lousy breaks in chemistry. Given the chance, I would design a world in which aluminum was as cheap and easy to weld as iron.
When I was in my teens trying to find a metal for lost-wax casting, I felt this way about all the metals I tried. I wanted one that melted easily, was runny so it flowed into detailed molds, didn't oxidize when molten, and, most important, could be found cheap at Marco's Scrap Metal. This last requirement eliminated tin, the best casting metal for kids (hence tin soldiers).
Lead is a lot like tin and also comes as scrap (car batteries), but it's horribly toxic (which made me worry every time I used it). Aluminum was out because it didn't fill the finer details in the mold, although I now realize I should have used old pistons, not old storm windows, as my raw material: Pistons are made through casting and thus contain an alloy conducive to the process.
Finally I settled on zinc. I could just barely melt it (420°C) on the kitchen stove (something I'd do while my mom was out so she wouldn't see me helping it along with a propane torch), and it was dirt cheap as roof flashing.
I made a lot of little castings using plaster of Paris molds and old candle wax. After casting plaster around a wax original, I baked out the wax and dried the mold in a toaster oven. (Big molds required the kitchen oven and more Mom's-away timing; this is a smoky process.)
I did my lost-wax casting crudely and without instructions, which is pretty much the way it was first done 6,000 years ago. The ancient and clever people of Mesopotamia (now Iraq) devised the process using charcoal fires and clay molds, but in essence they were doing the same thing I did, using what they had around them as best they could. Standing there in my basement, pot full of molten zinc, I felt closer to them than I ever could by reading a book or replicating their methods.
And in that spirit, I've been working to refine my techniques. Next month, the modern primitive method: how to melt metal in a microwave oven.
Scan of printed version:
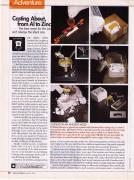 |
| |
| |
|
| |
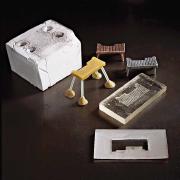
The various stages of lost-wax casting.
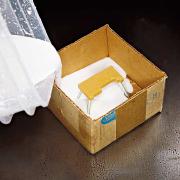
Plaster of Paris is poured around the wax model to form the mold.
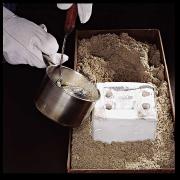
The molten zinc is poured into the now vacant mold.
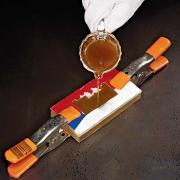
Melted beeswax is poured into a plastic mold, fashioned from casting resin, to create a mini periodic table.
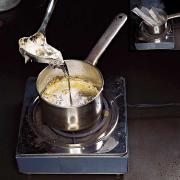
While the wax is baked out in a toaster oven, zinc is melted on an electric burner.

After the zinc has cooled, the mold is broken to reveal the metal casting.
Photo Credits: Jeff Sciortino Jeff Sciortino Jeff Sciortino Jeff Sciortino Jeff Sciortino Jeff Sciortino
|
|