|
| Plate your 'PodHow do you keep the back of your iPod clean? Sandpaper and electricity |
| |
| |
I think Apple sells fantastic objects that look like they came from the future. And apparently, in that future we all live in velvet rooms and have no fingers—there's no other way to explain the ultra-shiny mirrored backside of my new iPod nano, which got scratched and grungy with fingerprints in exactly three seconds. So I gave it a nifty scuff shield and, while I was at it, my own logo, using a superthin layer of electroplated copper.
Electroplating is usually done in factories for things like covering car bumpers in chrome, but the process is simple. An electric current runs through an object submerged in a chemical bath along with a strip of metal called the anode. The current rips electrons from the material of the anode, turning it slowly into metal ions. The ions travel through the bath and regain electrons at the surface of the object, where they turn back into solid metal. The net effect is to coat the object with metal taken from the anode: a shiny finish in two or three minutes.
But if the solution isn't just right, or the surface not correctly prepared, the thin layer of metal won't stick. Fortunately, today you can buy plating solutions that work well out of the bottle, and unlike in the past, most aren't cyanide-based.
I created my design using a custom rubber stamp ($12.50 at a laser-cutting shop) to apply ink to the back of the iPod. The ink blocks the current, leaving an outline of my pattern. To avoid dunking my new iPod in a chemical bath, I temporarily glued a bottomless miniature tank onto its back.
It took about 10 tries, but I finally got the plating to stick even while I scrubbed the ink off with acetone. Apple products may not be perfect, but with some sandpaper, glue, lasers, industrial chemicals and two AA batteries, you can fix them.
Scan of printed version:
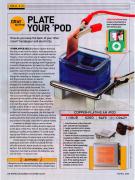 |
| |
| |
|
| |
|
|
|
|